https://www.myziyuan.com/
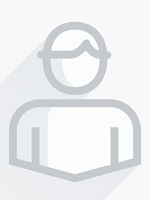
- 阿里
- 测量系统分析Measurement Systems Analysis一、测量系统所应具有之统计特性 测量系统必须处于统计控制中,这意味着测量系统中的变差只能是由于普通原因而不是由于特殊原因造成的。这可称为统开发者系统计稳定性 。测量系统的变差必须比制造过程的变差小 。变差应小于公差带 。测量精度应高于过程变差和公差带两者中精度较高者,一般来说,测量精度是过程变差和公差带两者中精度较高者的十分之一 。测量系统统计特性可能随被测项目的改变而变化。若真的如此,则测量系统的最大的变差应小于过程变差和公差带两者中的较小者 。二、标准 国家标准 第一级标准(连接国家标准和私人公司、科研机构等) 第二级标准(从第一级标准传递到第二级标准)工作标准(从第二级标准传递到工作标准) 三、测量系统的评定 测量系统的评定通常分为两个阶段,称为第一阶段和第二阶段 第一阶段:明白该测量过程并确定该测量系统是否满足我们的需要。第一阶段试验主要有二个目的 :确定该测量系统是否具有所需要的统计特性,此项必须在使用前进行 。发现哪种环境因素对测量系统有显着的影响,例如温度、湿度等,以决定其使用之空间及环境 。第二阶段的评定 目的是在验证一个测量系统一旦被认为是可行的,应持续具有恰当的统计特性 。常见的就是“量具R&R”是其中的一种型式 。四、各项定义 量具: 任何用来获得测量结果的装置,包括用来测量合格/不合格的装置 。测量系统:用来获得表示产品或过程特性的数值的系统,称之为测量系统。测量系统是与测量结果有关的仪器、设备、软件、程序、操作人员、环境的集合。量具重复性:指同一个评价人,采用同一种测量仪器,多次测量同一零件的同一特性时获得的测量值(数据)的变差。量具再现性:指由不同的评价人,采用相同的测量仪器,测量同一零件的同一特性时测量平均值的变差。稳定性:指测量系统在某持续时间内测量同一基准或零件的单一特性时获得的测量值总变差。偏倚:指同一操作人员使用相同量具,测量同一零件之相同特性多次数所得平均值与采用更精密仪器测量同一零件之相同特性所得之平均值之差,即测量结果的观测平均值与基准值的差值,也就是我们通常所称的“准确度”线性:指测量系统在预期的工作范围内偏倚的变化。五、分析时机 新生产之产品PV有不同时 新仪器,EV有不同时 新操作人员,AV有不同时 易损耗之仪器必须注意其分析频率 。R&R之分析 决定研究主要变差形态的对象 .使用「全距及平均数」或「变差数分析」方法对量具进行分析 .于制程中随机抽取被测定材料需属统一制程 .选2-3位操作员在不知情的状况下使用校验合格的量具分别对10个零件进行测量, 测试人员将操作员所读数据进行记录, 研究其重复性及再现性(作业员应熟悉并了解一般操作程序, 避免因操作不一致而影响系统的可靠度)同时评估量具对不同操作员熟练度. 试验完后, 测试人员将量具的重复性及再现性数据进行计算如附件一(R&R数据表), 附件二(R&R分析报告), 依公式计算并作成-R管制图或直接用表计算即可 结果分析 :当重复性(AV)变差值大于再现性(EV)时 .量具的结构需在设计增强.量具的夹紧或零件定位的方式(检验点)需加以改善 .量具应加以保养.当再现性(EV)变差值大于重复性(AV)时 .作业员对量具的操作方法及数据读取方式应加强教育, 作业标准应再明确订定或修订 .可能需要某些夹具协助操作员, 使其更具一致性的使用量具 .量具与夹治具校验频率于入厂及送修纠正后须再做测量系统分析, 并作记录 .测量系统R & R分析(均值—极差法)这里介绍常用的均值—极差法,用来研究测量系统的双性:R & R。它也称大样法(Long Method)。研究R & R的前提是测量系统已经过校准,而其偏倚、线性及稳定性已经过评价并认为可接受。
- 2021-12-15 01:59:12
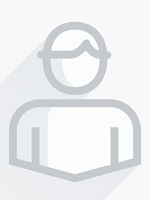
- 远古
- TS16949的五个工具工作学习日记2009-05-16 11:02 READ 53评论0字典:大中小TS16949五工具:APQP,PPAP,FMEA,MSA,SPC 1,APQP \u003d先进的产品质量规划产品质量专利计划是批准生产程序的参考指南,解释了产品设计和开发的整个过程,以采样生产,试验生产和生产控制计划。二,PPAP \u003d生产零件批准过程生产批准程序,生产生产,要求生产能力根据生产能力验证生产能力。PPAP产品提交:主要产品大小检测报告(FAI),外观检验报告(AAR),功能检验报告(本零件为客户提供原材料,其中大部分由客户组装),材料检验报告(SGS);加上一些部件控制方法和供应商控制方法,包括:失败ModE和效果分析(FMEA),制造工程质量控制计划(PMP,QC绘图),测量系统分析(MSA包含GR&& R),作业标准(SOP),检查标准(SIP),初始阶段过程容量分析(CPK)等;主要是制造企业要求供应商在提交产品时进行PPAP文件和第一(样本),只有当PPAP文件都是合格的,即正常交付(除非客户可以获得许可);该报告必须在工程变更后提交。PPAP是生产部件的控制程序和质量管理方法。这里,QA或QE的质量的一部分是:PMP,CPK,SIP,MSA和PSA(产品确认,产品确认),产品检测和测试。应提交的文件和报告是:1。设计记录2.任何授权工程变更文件(工程变更文件)3。在所需时,工程批准(客户工程批准)4。设计FMEA [单独#](设计FMEA)5.过程流程图6.过程FMEA [单独#](过程FMEA)7.尺寸结果8.材质&性能测试结果9.初始过程研究[新标题] 10.测量系统分析研究11.合格实验室(合格实验室文件)文件12控制计划13.零件提交权证(零件订阅)14。外观批准报告(外观批准报告,如果需要)15.散装物料req.Checklist 16.样品产品[单独#](发送零分量)确定的样品数)17.主样本#](标准样品/密封)18。检查艾滋病19.遵守客户的记录 - 具体要求(客户特定要求提交记录/有毒物质执行WSS-M99P9999-A1)/“otS报告)/(D / CC批准书面记录)(规格宣言) - CPK稳定过程CPK稳定Capk-稳定过程能力指数,据估计,估计PI-PPK-PPK - 性能指数基于整体恶化。指数值>1.67:该过程符合客户的要求,并可根据控制计划开始生产。1.67>指数值>1.33:该过程目前可接受,但需要进一步改进;应该与客户联系并分析研究结果。如果批量生产前没有改善,则需要修改控制计划。索引值<1.33:该过程无法满足验收标准。与适当的客户代表联系并评估结果。提交级别:供应商应根据客户所需提交水平的规定提交适当的材料和/或记录。第三,FMEA \u003d失效模式和效果分析失败模式和效果分析四,MSA \u003d测量系统分析测量系统分析它使用数学统计和图表到分析测量系统的错误,以评估测量系统的测量系统,确定测量系统错误的主要组件是合适的。通过测量系统分析,了解了所有生产过程的定量使用的恶化,分析了不合格的数量,改进,改进了检查,测量,测试数据真实性和报告的准确性;在测试中减少产品,测量,测试期间误判的可能性。在日常生产中,我们经常分析测量过程中获得加工组件过程的过程的过程的状态,能力和监测过程的过程;那么,如何确保分析结果是正确的?我们必须保证从两个方面保证,一个是确保测量数据的准确性/质量,评估通过测量数据获得的测量系统使用测量值ENT系统分析(MSA)方法;其次,确保适当的数据分析方法,例如使用SPC工具,测试设计,方差分析,回归分析等。MSA使用测量系统的方法来分析测量系统的分辨率和误差来评估测量系统的分辨率和错误,无论是适合测量的参数,并确定测量系统错误的主要组件。测量系统的误差的特点是测量在稳定条件下运行的测量系统中的数据:偏差和方差。偏置是指测量数据相对于标准值的位置,包括测量系统的偏差,线性和稳定性;并且部分差异是指数据的分散程度,也称为R&r,r&R,再现系统和再现包括测量系统的可重复性。在GE.NERAR,测量系统的分辨率应该非常多样化以获得获得测量参数的过程。测量系统的偏置和线性由量校准确定。测量系统的稳定性可以通过相同组件的相同部分的相同质量特性的平均极差控制图来监视。测量系统的可重复性和再现性由Gager&amp确定;R.分析使用的数据必须来自测量系统,具有适当的分辨率和测量系统错误,否则,无论我们使用什么样的分析方法,最终都会导致错误分析结果。在ISO10012-2和QS9000中,测量系统的质量保证具有相应的要求,要求公司有相关的程序来验证测量系统的有效性。MSA在企业中的应用:MARKET需要驾驶MSA应该是商业质量管理。随着越来越多的跨国公司进入中国市场投资厂,为了降低成本,他们都加快了购买本地化的过程。在选择和评估供应商时,这些公司非常重视供应商的质量保证体系,SPC(统计过程控制)和MSA的应用现状(测量系统分析)提供了产品的稳定产品。能力的重要参考指标。与此同时,这些成功的公司自己的实践还证明了SPC和MSA的成功是确保公司的质量保证体系稳定有效,提高了关键竞争力。为了在未来的市场竞争中获胜,许多市场意识高级公司在商业质量管理中实施了MSA,并增加了SPC应用程序。测量系统分析方法SIS:执行测量系统分析时,应采取最小化误导性结果的可能性:a)分析的测量系统应在验证(校准)有效期内;b)测量测量系统的重要性,并仔细仔细执行测量;c)执行GRR分析时,应以随机顺序测量,以确保整个研究过程中的任何变化是随机分布的。测量不应知道要测量的数量以避免可能的偏差。但是,这些组织测量系统分析应该知道正在检查哪个部件,并在“定量数据集数据表”或“计数测量系统分析报告”中相应地记录测量数据;d)计量测量应该估计读数尽可能准确,并且普通读数应采用最小规模的一半;e)计数的结果类型asuing工具,只读“接受”或“拒绝”,每个测量应该使用相同的方法,包括获得读数的所有步骤;g)当执行GRR分析时,人员测量系统分析应根据“数量再现性和可重复的数据表”中的数据计算,并且计算结果将填补测量系统分析“不同的重复性和再现性报告”分析每个劣化和整个测量系统的恶化过程的百分比;h)对于稳定性分析,记录的数据应该在Xbar-R控制图上绘制,然后分析,确定它是否处于失控或不稳定状态;i)对于计数类型测量工具,组织的测量系统分析基于“计数测量系统的分析”,填补评估结果。填写数据记录表:我使用的录制表样式可以对“测量系统分析”参考手册(版本3)进行渐变系统分析(MSA)。收集数据后的计算填充过程如下:(1)减去第一,2和3中的最大值以最小化它们的最小值;结果记录在第5行。在第6,7,12和13行中重复该步骤,并在第10行和15行记录结果;(2)将数据填充填充填充5,10和15;(3)添加第5行的数据并除以部分的数量,以获得第一操作员可怜的rbar的测量。还处理10th和第15行的数据以获得RB和RC;(4)将线条5,10和15到第17行的转动数据(RA,RB,RC),添加它们并将运算符的数量分开将被记录为R(所有差别的所有平均值);(5)摩擦(平均值)被掺入步骤19和20并乘以D3和D4,以获得控制下限和上限。注意:如果2个测试是进行,D3为零,D4为3.27。单个极端上限值(UCLR)被添加到第19行。低于7测量的控制下限值(LCLR)等于零;(6)对于大于UCLR的数据,相同的操作员应重新测量使用的部件,或消除这些值并循环平均值。基于改进的样本容量重新计算rbar和极限UCLR。纠正失控的特殊原因;(7)在线(第一,2,3,6,7,8,11,12和13)添加值。每行都在部件数量和部件数量的数量范围内(表1);(8)除了测试数量之外,还添加第一个,2和3行(最后一列)的平均值,结果填充了第四行的XA GEGE中。在第6,7和8,11,12和13线上重复该过程,结果分别填充Xb,XC,XB,XC(表1)。(9)将是14林的4,9和最大值和最低值ES(参考XA,XB,XC)填充在第18行的适当空间中。并确定它们的差异,填补标有XDIFF的第一行的差异(表1);(10)将每个部分添加到每个测量值并划分测量总数(测试号乘以运营商的数量)。在第16行零件XBAR的列中填充结果(表1)(11)使用最大部分平均值(XP)减去最小部分平均值(XP),并填充结果的第六线标签。空间。RP是零件平均值的差异(表1)(表1);(12)将16行的值添加到所有测量值的所有测量的总平均值;(13)计算报告表格列中RBAR,RP和XDIFF转移的计算值(表2);(14)桌子左侧“测量系统分析”下的计算;(15)计算桌子右侧的“总变化%”(16)检查结果S确认没有错误。测量系统的评估:人员分析了通过计算评估的测量系统分析的测量系统分析,在重复和可重复的报告中确定是否可以接受测量系统是否用于预期用途。V.SPC \u003d TIC过程控制过程容量的统计分析
- 2021-12-15 01:57:30
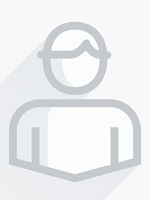
- gyq
- PPAP怎么做呀,以下是PPAP的程序文件,请参考. 1.目的 本程序明确规定了各生产件批准的各种必要的手续、分管部门及适用范围,以达到产品认定申请的规范化。在了解客户工程设计和规范所有要求的前提下,挖掘潜力,以在实际生产过程中按规定的生产节拍来生产满足客户要求的产品。 2.定义 生产件是指在生产现场使用生产工装、量具、过程、材料、操作者、环境和过程参数(如:进给量/速度/循环时间/压力/温度/湿度)制造的零件。生产件批准的零件取自有效的生产过程。该过程以1小时~8小时的生产,规定的产量至少为300件,除非客户另有书面通知。 3.范围 本文件适用于客户提出生产件批准要求的产品。在下述情况的第一批生产件发运前应进行生产件批准。 3•1首次交货的产品。 3•2因针对异常情况采取对策而更改设计的产品。 3•3因客户改变技术要求而更改设计的产品。 3•4为改进而更改设计的产品。 3•5用新的或改造后的设备、工模夹具进行生产的产品。 3•6现有设备、工模夹具进行后的的产品。 3•7制造工序或制造方法改变后生产的产品。 3•8制造车间或制造场所转移后生产的产品。 3•9材料零件的交货企业或产品加工企业变更。 3•10重新启用停用12个月以上的设备进行生产的产品。 3•11由于品质问题而中止交货的产品重新投产。 4.职责 4•1技术部负责编制零件提交保证书、产品测量与试验、过程能力调查、样品保管等工作。 4•2技术部负责确认技术条件、制订工艺流程图、编制过程FMEA和控制计划等。 4•3生产部负责批量产品的生产。 5.工作程序 5•1生产件批准所需的条件。 接受OS9000认证,符合第3项适用范围的产品,需提供下列文件资料。 5•1•1编制“零件提交的保证书”。 5•1•1•1 技术部确认所需资料,包括测量结果与试验结果,填在零件提交保证书中,然后交技术部经理。 5•1•1•2技术部经理确认测量结果和试验结果,资料齐全,符合生产件批准的要求,在保证书上签字。 5•1•2客户指定有外观项目时,编写“外观件批准报告”。 5•1•3技术部确认客户技术文件的内容与合同内的技术条件、尺寸图、外观要求等内容一致。 5•1•4在客户对技术要求内容进行更改情况下,技术部门要确认客户提出的文件或经更改的技术要求。 5•1•5生产部准备产品的2个样品,而且把用于尺寸测量(保留/提交要求表第6项尺寸结果)中的1件样品作为“标准样品”保管起来。 5•1•6生产部检验组按照客户技术文件中的尺寸图或由本公司提出经客户认可的尺寸图中注明的尺寸测量产品。测量的件数应符合客户的规定。 5•1•6•1经尺寸测量的产品,取其中的一件作为“4.1.5”中所述的“标准样品”保管起来,保管期限与“零件提交保证书”一致。 5•1•6•2对于提交产品,供方确认发运零件的重量,重量应在保证书上说明,用Kg表示并准确到小数点后四位。重量不包括运输时,包装箱、托盘等辅助材料(包装材料)。为了确定质量,随机选择10个零件称重,然后计算平均重量。 5•1•7为了便于检查试验,准备好检查用具。(检测仪器、标准件)。 5•1•8计量室根据客户技术文件的规定,进行材质试验,其中包括金相、硬度、化学元素等。试验数量应符合客户的规定。对于“3.范围”中各种生产件批准,当需要减少试验项目、更改试验数量时,应向客户的零件批准部门提出申请,并得到许可。 5•1•9技术部编制工艺流程图。 5•1•10技术部编制过程模式及后果分析(过程FMEA)。 5•1•11技术部制订所有零件和过程有关的重要或主要特性的控制计划。 5•1•12实施过程能力调查,进行评价,根据评价结果进行下列处理: 5•1•12•1生产部按照客户技术文件中有关性能、尺寸检查项目规定,进行过程能力调查。用于测量的产品依次排列,至少20组,每组5件,测量后绘 —R管理图,算出过程能力。根据管理图对过程的稳定性进行分析。 5•1•12•2根据过程能力的调查结果,作出与之相应的处理:当PpK(Pp)>1.67,符合客户所要求的条件。经客户批准后,由技术部用书面形式通知生产制造部开始生产。当1.33≤PpK(Pp)≤1.67时,与客户所要求的条件不符。制造部要特别小心,同时通过改进,将CpK(长期过程能力指数)提高到1.33以上,并向技术部通报。技术部确认改进状况,报客户认定后,再以书面形式通知生产制造部开始生产。当PpK(Pp)≤1.33时,低于客户要求的水准。必须进行过程改进并形成纠正措施计划文件。增加检验或试验,有时,采取全数检查的方法,再由客户认定。经认定后,再用书面形式通知生产部门开始生产。 5•1•13检测中心编写测量系统变差分析报告。 5•1•14当客户技术文件(包括附图)中存在着需要经客户的设计部门批准的事项时,技术部要在提出“零件提交保证书”前,预先获得认定。 5•2申请等级 在保管生产件批准所需的文件时,应符合客户指定的下列等级。 当客户未指定申请等级时,按等级3级执行。 保留/提交要求表 要 求 申 请 等 级 等级1 等级2 等级3 等级4 等级5 1.保证书 S S S S R 2.外观件批准报告 S S S S R 3.样品 R S S R R 标准样品 R R R R R 4.设计图技术要求 R S S S R R S* S* S* R 5.更改文件(如果有) R S S S R 6.尺寸结果 R S S S R 7.检查用具 R R** R** R R 8.试验结果 R S S S R 9.过程流程图 R R S S R 10.过程FMEA R R S S R 设计FMEA R# R# S# S# R# 11.控制计划 R R S S R 12.过程能力研究 R R S S R 13.测量系统研究 R R S S R 14.设计工程批准 R R S S R S—提交给指定的客户零件批准部门。在制造厂只存复印件。 R—在制造厂保留,客户代表有要求时易于取得。 *—除非客户放弃。 **—根据客户要求提交。 #—适用于供方有设计职责的情况。 提交等级分别是: 等级1—只向客户提交保证书(对指定外观项目,还应提交一份外观件批准报告); 等级2—向客户提交保证书和零件样品及有限的支持数据; 等级3—向客户提交保证书和零件样品及完整的支持数据; 等级4—向客户提交保证书和完整的支持数据(不含零件样品); 等级5—在供方制造厂评审完整的支持数据和零件样品。 每一个等级的确切要求详见保留/提交要求表。 由5•1项完成的文件、数据资料等原件,由编制部门作为质量记录登记、保管。 5•3产品提交 产品在未接到客户批准前,决不按批量发运其产品。 5•3•1生产件批准指产品满足客户所有的规范和要求,可按合同安排批量发运。 5•3•2临时批准指允许按限定时间或产品数量运送生产需要的产品,当产品不能获得批准时,技术部在明确了影响生产件批准的不合格的根本原因,提出纠正措施后,申请临时批准。临时批准出厂的产品,按客户的规定办理手续。 6.相关文件 6•1 QS/TSB 20201—2002 产品质量先期策划控制程序 6•2 QS/TSB 20202—2002 过程FMEA控制程序 6•3 QS/TSB 22001—2002 统计技术选择与应用程序 7.相关表格
- 2021-12-15 01:57:30